Activity Based Costing Abc Method And Advantages Defined With Example
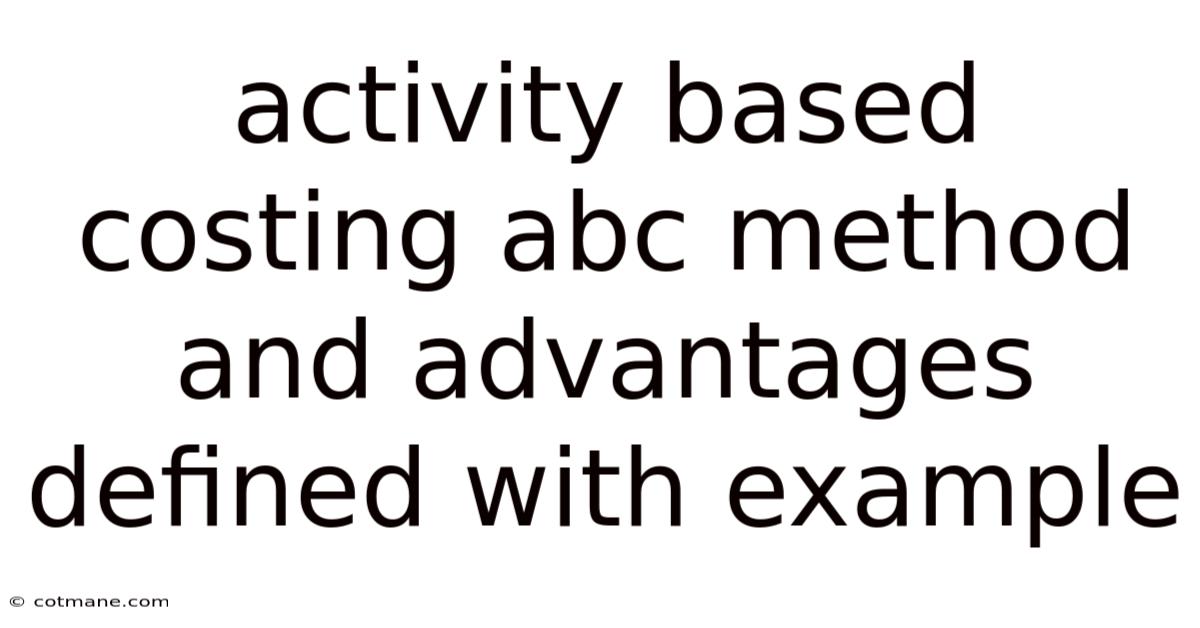
Discover more detailed and exciting information on our website. Click the link below to start your adventure: Visit Best Website meltwatermedia.ca. Don't miss out!
Table of Contents
Activity-Based Costing (ABC) Method: Unveiling the True Cost of Products and Services
What makes activity-based costing (ABC) a game-changer in today’s landscape?
Activity-Based Costing (ABC) is revolutionizing cost accounting, offering unparalleled accuracy and insights into product and service profitability.
Editor’s Note: Activity-Based Costing (ABC) has been updated today.
Why Activity-Based Costing Matters
Traditional cost accounting methods, such as absorption costing, often allocate overhead costs based on simplistic measures like direct labor hours or machine time. This can lead to significant distortions in product costing, especially in businesses with diverse product lines and complex manufacturing processes. Activity-Based Costing (ABC) offers a more refined approach, directly linking costs to the activities that drive them. This enhanced accuracy provides crucial information for pricing strategies, product mix decisions, process improvement initiatives, and overall profitability analysis. Understanding the true cost of producing each product or delivering each service is paramount for informed business decisions in today's competitive environment. ABC's impact extends beyond manufacturing; it is increasingly adopted in service industries like healthcare, finance, and consulting where overhead allocation can be particularly challenging.
Overview of the Article
This article explores the key aspects of Activity-Based Costing (ABC), its practical applications, and its growing influence across diverse industries. Readers will gain a comprehensive understanding of ABC's methodology, its advantages over traditional methods, and its application through detailed examples. Furthermore, the article will address common challenges and misconceptions associated with implementing ABC. The ultimate goal is to equip readers with the knowledge and insights necessary to assess the suitability of ABC for their specific organizational context.
Research and Effort Behind the Insights
This article is based on extensive research, incorporating insights from leading cost accounting textbooks, academic journals, and industry best practices. Numerous case studies and examples are used to illustrate the practical application of ABC and its impact on businesses. The information presented reflects a thorough understanding of the ABC methodology and its implications for modern cost management.
Key Takeaways
Key Aspect | Description |
---|---|
ABC Methodology | Identifies and assigns costs based on activities, not simply volume-based drivers. |
Cost Pool Creation | Groups costs associated with specific activities (e.g., machine setup, quality control, order processing). |
Cost Driver Identification | Determines the factors driving the cost of each activity (e.g., number of setups, number of inspections). |
Cost Allocation | Assigns costs from cost pools to products/services based on their consumption of cost drivers. |
Improved Accuracy | Provides a more accurate reflection of product/service costs, leading to better pricing and profitability analysis. |
Enhanced Decision-Making | Facilitates informed decisions regarding pricing, product mix, process improvement, and resource allocation. |
Smooth Transition to Core Discussion
Let's dive deeper into the key aspects of Activity-Based Costing (ABC), starting with its foundational principles and illustrating its application through a detailed example.
Exploring the Key Aspects of Activity-Based Costing (ABC)
-
Understanding ABC's Core Principles: ABC departs from traditional cost accounting by focusing on activities as the primary cost drivers. Instead of allocating overhead costs based on simple volume measures, ABC identifies specific activities involved in producing a product or service. These activities are grouped into "cost pools," and costs within each pool are allocated based on the consumption of "cost drivers." Cost drivers are factors that determine the level of activity and, consequently, the cost incurred.
-
Identifying and Grouping Activities: This is a crucial first step. A thorough analysis of the production or service delivery process is required to identify all significant activities. Examples include machine setups, material handling, quality inspections, engineering design, customer service calls, and administrative tasks. Similar activities are then grouped into cost pools. The more finely activities are identified, the more accurate the cost allocation will be.
-
Assigning Costs to Cost Pools: Once activities are grouped, the costs associated with each activity are assigned to the respective cost pools. This includes direct labor, materials, and overhead costs directly attributable to that activity. For example, the cost pool for "machine setup" would include the labor cost of setting up the machine, the cost of any specialized tooling, and a portion of the machine's depreciation.
-
Determining Cost Drivers: The next step involves identifying the appropriate cost driver for each cost pool. This is the factor that most accurately reflects the consumption of resources by each product or service. For example, the number of setups might be the cost driver for the "machine setup" cost pool, while the number of inspections might be the cost driver for the "quality control" cost pool.
-
Allocating Costs to Products/Services: Finally, costs are allocated to individual products or services based on their consumption of the cost drivers. For example, if Product A requires 10 setups and Product B requires 5 setups, and the total cost of the "machine setup" cost pool is $10,000, then $6,667 would be allocated to Product A and $3,333 to Product B ($10,000 / 15 setups * respective number of setups). This process is repeated for each cost pool, and the total cost of each product or service is the sum of its direct costs and allocated overhead costs.
Closing Insights
Activity-Based Costing (ABC) is a powerful tool for accurate cost allocation, offering businesses crucial insights into product profitability and operational efficiency. Its ability to move beyond simplistic volume-based cost drivers allows for a far more nuanced understanding of the cost structure, enabling informed decision-making across various aspects of the business.
Exploring the Connection Between Overheads and Activity-Based Costing
Traditional costing methods often struggle to accurately allocate overhead costs. Overhead, encompassing indirect costs like rent, utilities, and administrative expenses, is often assigned using arbitrary allocation bases, leading to distorted product costs. ABC addresses this by directly linking overhead costs to specific activities. For example, rent might be allocated based on the square footage used by each production department, reflecting the activity of utilizing space. By connecting overhead to activities, ABC provides a more precise and realistic picture of the true cost of products and services. This improved accuracy is particularly valuable in environments with complex product lines or diverse service offerings.
Further Analysis of Overhead Allocation in ABC
Traditional Method | Activity-Based Costing |
---|---|
Arbitrary Allocation (e.g., direct labor hours) | Activity-specific allocation based on cost drivers (e.g., machine hours, number of orders) |
Potential for Cost Distortion | Reduced cost distortion, more accurate reflection of product/service costs |
Limited Insight into Cost Drivers | Detailed understanding of cost drivers and their impact on overall costs |
Less Effective Decision Support | Improved decision support for pricing, product mix, process improvement, and resource allocation |
Example: Manufacturing Company
Let's consider a manufacturing company producing two products, Product A and Product B. Both products use the same machines and share similar overhead costs. Under traditional costing, overhead might be allocated based on machine hours, resulting in a distorted cost picture if one product requires more complex setups or inspections than the other.
Using ABC, the company identifies activities like machine setup, quality control, and material handling. Each activity forms a cost pool, and cost drivers are identified for each pool (e.g., number of setups for the machine setup pool, number of inspections for the quality control pool). Costs are then allocated based on each product's consumption of these cost drivers. This results in a more accurate cost for each product, revealing the true profitability of each. For instance, if Product A requires significantly more setups than Product B, ABC will correctly allocate a larger portion of the machine setup costs to Product A.
FAQ Section
-
What are the limitations of ABC? Implementing ABC can be time-consuming and costly, requiring detailed analysis of activities and cost drivers. It also requires significant upfront investment in data collection and tracking systems.
-
Is ABC suitable for all businesses? ABC is most beneficial for businesses with complex production processes, diverse product lines, and significant overhead costs. Smaller businesses with simpler operations might find the cost and effort of implementing ABC outweigh the benefits.
-
How does ABC differ from traditional costing? Traditional costing uses simple allocation bases (e.g., direct labor hours) while ABC links costs to specific activities and their respective cost drivers.
-
What are the key benefits of ABC? Improved cost accuracy, enhanced decision-making, better understanding of cost drivers, and improved profitability analysis.
-
How does ABC improve pricing decisions? By providing a more accurate cost, ABC allows for more effective pricing strategies, ensuring products are priced to reflect their true cost and generate desired profit margins.
-
Can ABC be used in service industries? Absolutely! ABC is increasingly used in service industries, adapting the activity identification and cost driver selection to the specific characteristics of service delivery.
Practical Tips
-
Identify all significant activities: Conduct a thorough analysis of your production or service delivery process.
-
Group similar activities into cost pools: Ensure that activities within each cost pool share similar cost drivers.
-
Select appropriate cost drivers: Choose cost drivers that accurately reflect the consumption of resources by each product or service.
-
Collect accurate cost data: Establish robust data collection and tracking systems to ensure accurate cost allocation.
-
Regularly review and update your ABC system: Your activities and cost drivers may change over time, so regular review and updates are essential.
-
Use software to streamline the process: Specialized software can automate many of the steps involved in ABC, reducing manual effort and improving accuracy.
-
Train your staff: Ensure that your staff understands the ABC methodology and how to use the information it provides.
-
Communicate the results effectively: Clearly communicate the findings of your ABC analysis to relevant stakeholders to ensure buy-in and effective use of the information.
Final Conclusion
Activity-Based Costing (ABC) represents a significant advancement in cost accounting, providing a far more accurate and insightful approach to understanding product and service costs. Its ability to connect costs directly to activities and their drivers allows for better pricing decisions, improved operational efficiency, and ultimately, enhanced profitability. While implementing ABC may require an initial investment of time and resources, the long-term benefits in terms of improved accuracy and decision-making make it a valuable tool for businesses seeking to optimize their cost structures and gain a competitive edge. Continued exploration of ABC's applications and refinement of its methodology will undoubtedly shape the future of cost management.
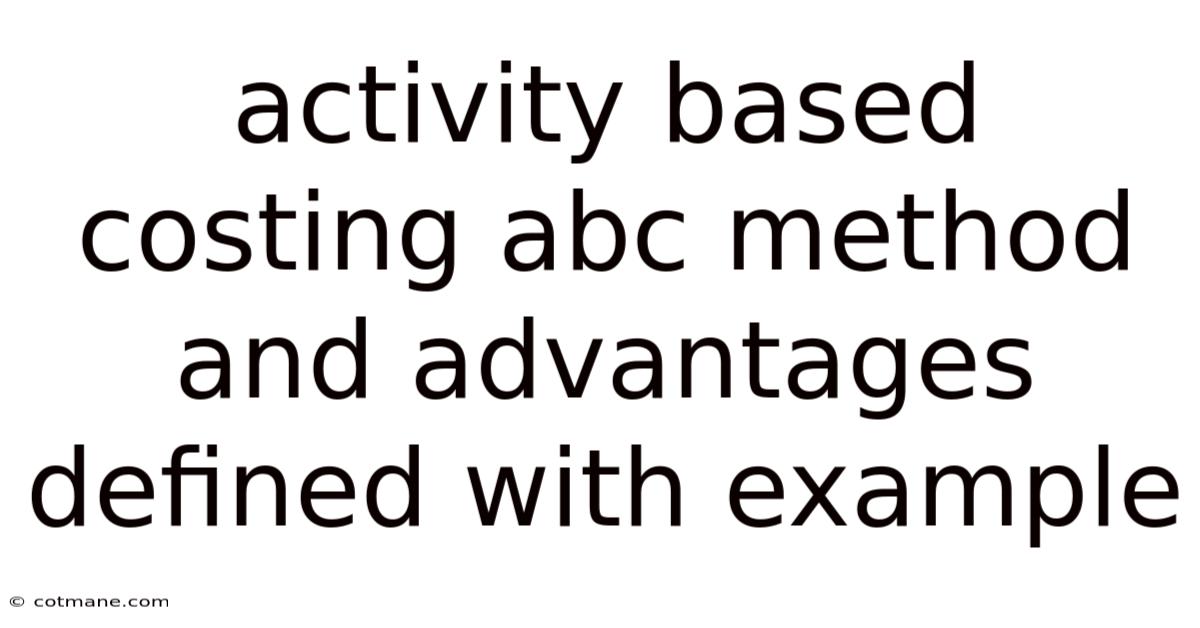
Thank you for visiting our website wich cover about Activity Based Costing Abc Method And Advantages Defined With Example. We hope the information provided has been useful to you. Feel free to contact us if you have any questions or need further assistance. See you next time and dont miss to bookmark.
Also read the following articles
Article Title | Date |
---|---|
Acceptance Testing Definition Types And Examples | Apr 04, 2025 |
Adjustable Rate Preferred Stock Arps Definition | Apr 04, 2025 |
All Cash All Stock Offer Definition Downsides Alternatives | Apr 04, 2025 |
Anatolian Tiger Definition | Apr 04, 2025 |
Aging Schedule Definition How It Works Benefits And Example | Apr 04, 2025 |