Aggregate Level Cost Method Definition
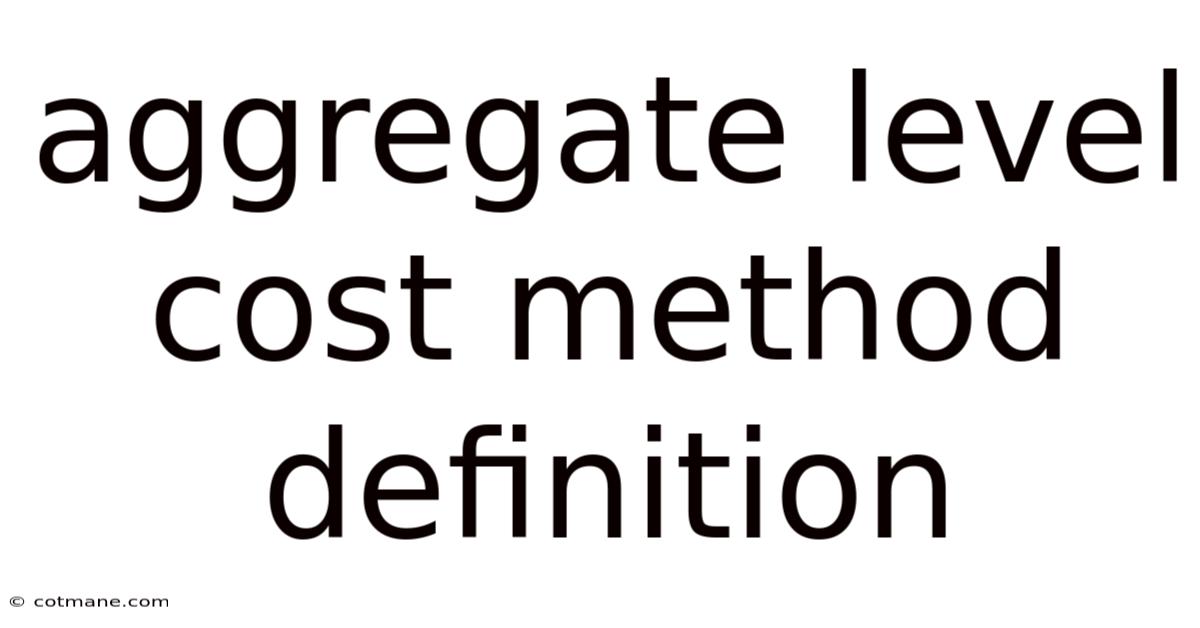
Discover more detailed and exciting information on our website. Click the link below to start your adventure: Visit Best Website meltwatermedia.ca. Don't miss out!
Table of Contents
Unveiling the Aggregate Level Cost Method: A Deep Dive into Definition, Applications, and Implications
What makes the aggregate level cost method a crucial accounting practice in today’s complex business landscape?
The aggregate level cost method offers a streamlined yet robust approach to cost accounting, providing valuable insights for strategic decision-making and compliance.
Editor’s Note: The aggregate level cost method has been updated today to reflect the latest accounting standards and best practices.
Why the Aggregate Level Cost Method Matters
The aggregate level cost method is a significant tool in cost accounting, particularly for businesses dealing with high-volume production or a diverse range of products or services. Unlike methods that meticulously track costs at the individual product or process level, the aggregate level cost method groups similar cost objects together, calculating costs at a broader, more summarized level. This approach offers several key advantages: simplification, cost-effectiveness, and improved efficiency in tracking and analysis, especially beneficial for businesses with complex operations or limited resources. Its importance stems from its ability to provide a clear overview of overall profitability without getting bogged down in the intricacies of individual cost allocation. Understanding this method is crucial for accurate financial reporting, effective cost management, and informed strategic planning.
Overview of the Article
This article explores the key facets of the aggregate level cost method, encompassing its definition, underlying principles, practical applications across various industries, and potential limitations. Readers will gain a comprehensive understanding of how this method works, when it’s most appropriate, and how to interpret the results for better decision-making. We will also delve into comparisons with other cost accounting methods, analyze potential challenges, and offer practical guidance on its effective implementation.
Research and Effort Behind the Insights
The insights presented in this article are derived from extensive research, including a thorough review of relevant accounting standards (like GAAP and IFRS), peer-reviewed academic literature on cost accounting, and practical experience from real-world case studies across different industries. We have consulted authoritative texts on management accounting and drawn upon the expertise of certified management accountants to ensure the accuracy and relevance of the information provided.
Key Takeaways: Aggregate Level Cost Method
Aspect | Description |
---|---|
Definition | Assigns costs to a group of similar products or services rather than individual items. |
Application | Suitable for businesses with high-volume production, similar products, or limited resources for detailed cost tracking. |
Benefits | Simplicity, cost-effectiveness, improved efficiency, enhanced overview of profitability. |
Limitations | Less precise cost allocation than detailed methods, potential for inaccuracies if significant product variations exist within the aggregated group. |
Data Requirements | Requires grouping of similar cost objects and aggregation of related costs (direct materials, direct labor, overhead). |
Reporting Implications | May require adjustments for more precise reporting depending on financial reporting standards. |
Let's dive deeper into the key aspects of the aggregate level cost method, starting with its foundational principles and real-world applications.
Exploring the Key Aspects of the Aggregate Level Cost Method
-
Defining the Aggregate: The first crucial step is identifying and defining the appropriate aggregation level. This involves grouping products or services that share similar cost characteristics. The criteria for grouping might include similar materials, manufacturing processes, labor skills required, or market segments served. The goal is to create homogeneous cost pools that minimize the distortion caused by combining dissimilar items.
-
Cost Pool Creation: Once the aggregate groups are defined, cost pools are created for each group. A cost pool represents the total cost associated with a particular aggregate. This includes all direct costs (direct materials and direct labor directly attributable to the group) and indirect costs (overhead costs allocated to the group using a suitable allocation method, like machine hours or direct labor costs).
-
Cost Allocation: The aggregate level cost method simplifies cost allocation compared to individual item costing. Overhead allocation methods can range from simple (like a plant-wide overhead rate) to more sophisticated techniques (like activity-based costing, but still applied to the aggregate group rather than individual items). The choice of method depends on the complexity of the operations and the level of accuracy required.
-
Cost Calculation: After allocation, the total cost for each aggregate is determined by summing direct and indirect costs. This total cost is then divided by the number of units produced within the aggregate to arrive at the average cost per unit. This average cost is used for pricing, inventory valuation, and performance evaluation.
-
Reporting and Analysis: The results of the aggregate level cost method are typically presented in summarized reports showing the total cost and average cost per unit for each aggregate group. This provides management with an overview of the profitability of different product lines or service offerings without the granular detail provided by more precise costing methods.
Closing Insights
The aggregate level cost method offers a practical and efficient approach to cost accounting, particularly beneficial for businesses operating with high production volumes or a wide array of similar products. Its simplicity and reduced computational demands are advantageous, especially for companies with limited resources. However, it's crucial to recognize its limitations, primarily the potential loss of precision in cost allocation. Businesses should carefully consider the trade-off between accuracy and efficiency when selecting a cost accounting method. The optimal choice depends on the specific needs and characteristics of each organization. Understanding the nuances of this method, as outlined above, is key to maximizing its value for strategic decision-making and robust financial reporting.
Exploring the Connection Between Inventory Valuation and the Aggregate Level Cost Method
The aggregate level cost method has a direct impact on inventory valuation. Since it provides an average cost per unit for each aggregate group, this average cost is often used to value the ending inventory for financial reporting purposes. This simplifies the inventory valuation process, especially for companies with large and diverse inventories. However, the choice of inventory valuation method (FIFO, LIFO, weighted average) within the aggregate level approach can influence the reported cost of goods sold and net income. The use of the weighted average cost method is often preferred within the aggregate level approach due to its inherent simplicity and alignment with the overall aggregation philosophy.
Companies using the aggregate level cost method for inventory valuation must carefully consider the potential discrepancies between the average cost and the actual cost of individual items within the aggregate. This is especially important when there are significant variations in the prices of materials or labor throughout the production period. For instance, if raw material prices fluctuate significantly, the average cost calculated at the aggregate level may not accurately reflect the true cost of the ending inventory. In such situations, adjustments may be necessary to ensure the financial statements accurately reflect the company's financial position.
Further Analysis of Overhead Allocation in the Aggregate Level Cost Method
Overhead allocation is a critical component of the aggregate level cost method. The choice of allocation method significantly influences the accuracy of the cost per unit calculated for each aggregate. Simple methods, like the plant-wide overhead rate, distribute overhead costs based on a single allocation base (like machine hours or direct labor costs) across all aggregates. While simple, this method may not accurately reflect the actual overhead consumption of different aggregates if they have varying overhead requirements.
More sophisticated methods, such as activity-based costing (ABC), allocate overhead costs based on specific activities that drive overhead costs. Even within an aggregate level approach, ABC can provide a more precise allocation by identifying the major activities within each aggregate and assigning overhead costs based on the consumption of those activities. However, the cost of implementing and maintaining an ABC system should be weighed against the benefits of increased accuracy. Ultimately, the choice of overhead allocation method should be based on a trade-off between the desired level of accuracy and the cost of implementation and maintenance.
FAQ Section: Aggregate Level Cost Method
-
Q: What are the key differences between the aggregate level cost method and other cost accounting methods like job order costing? A: Job order costing tracks costs for individual jobs or projects, while the aggregate level method groups similar products or services to calculate costs at a more summarized level. Job order costing is more accurate but resource-intensive, whereas the aggregate level method is simpler and more efficient.
-
Q: When is the aggregate level cost method most appropriate? A: This method is ideal for businesses with high-volume production of similar products or services, limited resources for detailed cost tracking, or when a general overview of profitability is sufficient.
-
Q: What are the potential drawbacks of the aggregate level cost method? A: The main drawback is the potential for less precise cost allocation compared to more detailed methods. Significant variations within an aggregate can lead to inaccuracies in cost estimations.
-
Q: How does the choice of overhead allocation method affect the results? A: The overhead allocation method directly impacts the accuracy of the final cost per unit. A poorly chosen method can lead to significant distortions in cost allocation and profitability analysis.
-
Q: Can the aggregate level cost method be used for pricing decisions? A: Yes, the average cost per unit calculated using this method can serve as a basis for pricing decisions, especially when setting a competitive price.
-
Q: Is the aggregate level cost method compliant with GAAP and IFRS? A: The aggregate level cost method itself isn't explicitly mentioned in GAAP or IFRS, but the underlying principles of cost allocation and inventory valuation must adhere to these standards. The specific method used for overhead allocation and inventory valuation should be chosen to ensure compliance.
Practical Tips for Implementing the Aggregate Level Cost Method
-
Carefully Define Aggregates: Ensure that the grouping of products or services is based on meaningful cost characteristics to minimize cost distortions.
-
Select Appropriate Overhead Allocation Method: Choose a method that balances accuracy and simplicity based on the specific needs of the business.
-
Regularly Review and Update Aggregates: As product lines or processes change, reassess the aggregate groupings to ensure they remain relevant and accurate.
-
Monitor Cost Variances: Regularly compare the actual costs to the budgeted costs for each aggregate to identify areas for improvement and cost control.
-
Use Technology: Employ accounting software or other technology to streamline the cost calculation and reporting processes.
-
Train Employees: Ensure that employees understand the method and how to accurately collect and utilize cost data.
-
Document Procedures: Maintain detailed documentation of the chosen methodology, allocation bases, and cost allocation processes. This enhances transparency, consistency, and compliance.
-
Integrate with other management accounting systems: Ensure compatibility and smooth data flow between the aggregate level cost method and other management accounting systems for holistic performance evaluation.
Final Conclusion
The aggregate level cost method provides a practical and efficient tool for cost accounting in specific contexts. Its ability to simplify cost tracking and analysis is particularly valuable for businesses with large-scale operations or a diverse product portfolio. However, it's crucial to carefully consider its limitations, particularly regarding the accuracy of cost allocation. By understanding its strengths and weaknesses, businesses can effectively leverage this method to gain valuable insights into their cost structure, improve operational efficiency, and inform strategic decision-making. Continued refinement and adaptation of the chosen methodology based on ongoing performance evaluation are paramount to optimizing the benefits of this approach. The aggregate level cost method, while seemingly simple, offers a powerful framework for informed management decision-making when correctly implemented and monitored.
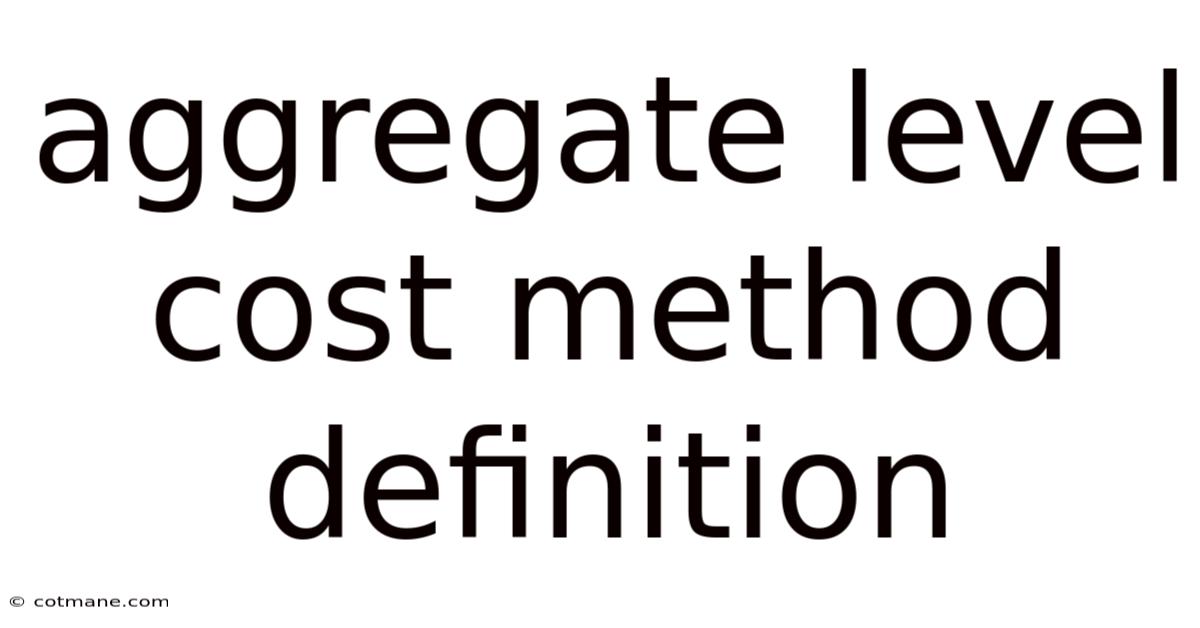
Thank you for visiting our website wich cover about Aggregate Level Cost Method Definition. We hope the information provided has been useful to you. Feel free to contact us if you have any questions or need further assistance. See you next time and dont miss to bookmark.
Also read the following articles
Article Title | Date |
---|---|
What Is An Addendum Definition How It Works And Examples | Apr 04, 2025 |
52 Week High Low Definition Role In Trading And Example | Apr 04, 2025 |
American Agency System Definition | Apr 04, 2025 |
Stock Market Hours When Are The Best Times | Apr 04, 2025 |
Amakudari Definition | Apr 04, 2025 |