What Are Direct Materials In Accounting
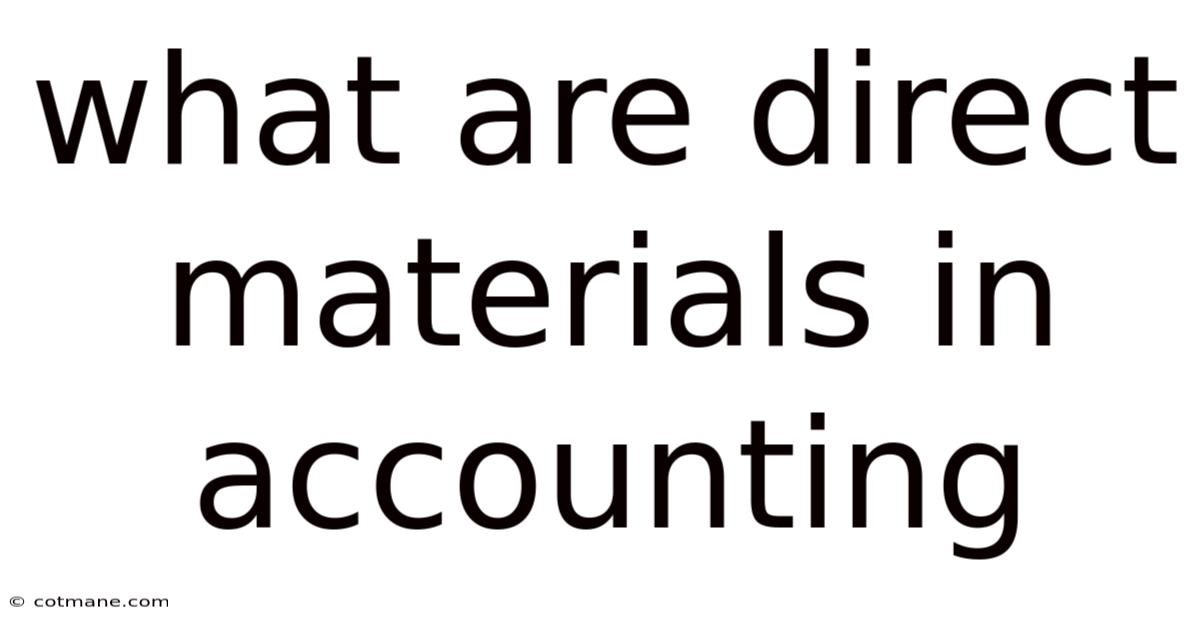
Discover more detailed and exciting information on our website. Click the link below to start your adventure: Visit Best Website meltwatermedia.ca. Don't miss out!
Table of Contents
Decoding Direct Materials in Accounting: A Comprehensive Guide
What makes understanding direct materials a cornerstone of accurate accounting?
Mastering direct materials accounting is crucial for precise cost allocation, informed decision-making, and ultimately, business profitability.
Editor’s Note: This comprehensive guide to direct materials in accounting has been published today.
Why Direct Materials Matter
In the world of accounting, understanding direct materials is paramount. Direct materials are the raw materials that are directly used in the production process and become an integral part of the finished goods. Their accurate accounting is essential for several reasons:
-
Costing Accuracy: Properly identifying and costing direct materials forms the bedrock of accurate product costing. This, in turn, impacts pricing strategies, profitability analysis, and inventory management. Inaccurate costing can lead to mispricing, loss of market share, and ultimately, financial instability.
-
Inventory Management: Effective tracking of direct materials is crucial for maintaining optimal inventory levels. Too much inventory ties up capital, while too little can lead to production delays and lost sales. Understanding the consumption patterns of direct materials allows for better forecasting and proactive inventory management.
-
Financial Reporting: Accurate recording of direct materials is a fundamental requirement for complying with generally accepted accounting principles (GAAP) and International Financial Reporting Standards (IFRS). This ensures transparency and reliability in financial statements, crucial for investors, lenders, and other stakeholders.
-
Decision-Making: Data on direct materials consumption, costs, and trends inform vital business decisions. This includes strategic sourcing, process improvement, and pricing strategies. Accurate data enables informed decisions leading to increased efficiency and profitability.
-
Compliance and Audits: Maintaining accurate records of direct materials is essential for successful audits and compliance with various regulatory requirements. This minimizes the risk of penalties and ensures the integrity of the financial reporting process.
Overview of the Article
This article provides a detailed exploration of direct materials in accounting. It will cover the definition and identification of direct materials, their accounting treatment, cost allocation methods, inventory management techniques related to direct materials, and the importance of accurate record-keeping. Readers will gain a comprehensive understanding of the significance of direct materials and their impact on the overall financial health of a business.
Research and Effort Behind the Insights
This article is the culmination of extensive research, drawing on authoritative accounting textbooks, industry best practices, and real-world examples. The information presented is based on established accounting principles and aims to provide readers with a clear and practical understanding of direct materials accounting.
Key Takeaways
Key Concept | Description |
---|---|
Definition of Direct Materials | Raw materials directly traceable to the finished product and easily identifiable within the production process. |
Cost Allocation | Methods to assign the cost of direct materials to the finished goods, such as FIFO, LIFO, and weighted average. |
Inventory Management | Techniques to optimize inventory levels, minimizing waste and maximizing efficiency. |
Record-Keeping | Accurate and meticulous record-keeping is crucial for accurate costing and financial reporting. |
Impact on Profitability | Accurate direct materials accounting directly influences product pricing and overall profitability. |
Let’s dive deeper into the key aspects of direct materials accounting, starting with its foundational principles and real-world applications.
Exploring the Key Aspects of Direct Materials Accounting
-
Defining Direct Materials: Direct materials are those raw materials that are directly used in the production process and can be easily traced to the finished product. This differs from indirect materials, which are used in the production process but are not directly traceable to specific products (e.g., lubricants, cleaning supplies). The key differentiator is traceability and direct incorporation into the final product. For example, in a furniture manufacturing company, the wood used to make a table is a direct material, while the glue and sandpaper used in the process are indirect materials.
-
Accounting for Direct Materials: The accounting treatment of direct materials involves tracking their acquisition, storage, and usage in the production process. This typically involves using inventory accounts, such as Raw Materials Inventory, Work-in-Process (WIP) Inventory, and Finished Goods Inventory. The costs associated with acquiring direct materials, including purchase price, freight, and handling charges, are recorded in the Raw Materials Inventory account. As materials are used in production, their cost is transferred to the WIP Inventory account. Once the goods are completed, the cost of direct materials is transferred to the Finished Goods Inventory account, and finally, to the Cost of Goods Sold (COGS) account when the goods are sold.
-
Cost Allocation Methods: Several methods are used to allocate the cost of direct materials to finished goods. The most common methods include:
- First-In, First-Out (FIFO): This method assumes that the oldest inventory items are sold first.
- Last-In, First-Out (LIFO): This method assumes that the newest inventory items are sold first. LIFO is allowed under US GAAP but not under IFRS.
- Weighted-Average Cost: This method calculates the average cost of all inventory items and assigns this average cost to the goods sold. The choice of method impacts the cost of goods sold and the value of ending inventory, affecting the company's profitability and financial statements.
-
Inventory Management Techniques: Effective inventory management is critical for optimizing direct materials usage and minimizing waste. Techniques such as Just-In-Time (JIT) inventory, Economic Order Quantity (EOQ), and Material Requirements Planning (MRP) are employed to ensure that the right amount of materials is available at the right time, minimizing storage costs and preventing stockouts.
-
Record-Keeping and Internal Controls: Maintaining accurate and detailed records of direct materials is essential for effective cost control and financial reporting. Robust internal controls are vital to prevent theft, loss, and inaccurate accounting. This includes proper documentation of purchases, receiving, storage, and usage, along with regular inventory counts and reconciliations.
Closing Insights
Direct materials accounting is not simply a technical exercise; it's a crucial element of effective financial management. Accurate costing, informed decision-making, and proactive inventory management directly impact a company's profitability and competitiveness. By understanding and applying the principles outlined in this guide, businesses can optimize their operations, reduce costs, and enhance their bottom line. The impact extends beyond mere accounting; it shapes strategic decisions related to sourcing, production, and pricing, ultimately influencing the company's overall success.
Exploring the Connection Between Waste Reduction and Direct Materials
Waste reduction initiatives are intrinsically linked to effective direct materials management. Minimizing waste translates directly into cost savings, improved efficiency, and a stronger environmental stance. By implementing robust inventory control systems, optimizing production processes, and embracing lean manufacturing principles, companies can significantly reduce material waste and enhance their profitability. The impact is not just financial; it also contributes to a more sustainable business model. For example, a company that implements a JIT system minimizes storage costs and reduces the risk of obsolescence, directly impacting its direct materials costs.
Further Analysis of Waste Reduction
Waste Reduction Strategy | Description | Impact on Direct Materials Costs | Example |
---|---|---|---|
Lean Manufacturing | Streamlines production processes to eliminate waste and improve efficiency. | Reduced material usage and waste | Implementing 5S methodology in a factory |
Just-In-Time (JIT) Inventory | Delivers materials only when needed, minimizing storage costs and reducing obsolescence. | Lower inventory holding costs | Automotive parts supplier using JIT delivery |
Improved Quality Control | Reduces defects and rework, minimizing the use of materials in flawed products. | Reduced material scrap and rework | Implementing stricter quality checks in production |
Material Substitution | Using alternative materials that are more cost-effective and environmentally friendly. | Lower material costs | Substituting plastic for wood in furniture |
Process Optimization | Identifying and eliminating inefficiencies in the production process. | Reduced material waste | Streamlining a packaging process to reduce waste |
FAQ Section
-
What is the difference between direct and indirect materials? Direct materials are directly incorporated into the finished product and are easily traceable. Indirect materials are used in the production process but are not directly traceable to specific products.
-
How are direct materials costs allocated? Several methods exist, including FIFO, LIFO, and weighted average cost. The choice depends on various factors, including company policy and industry norms.
-
Why is accurate record-keeping of direct materials crucial? Accurate record-keeping is essential for accurate costing, inventory management, financial reporting, and compliance with accounting standards.
-
What are some common inventory management techniques for direct materials? Just-in-Time (JIT), Economic Order Quantity (EOQ), and Material Requirements Planning (MRP) are common techniques.
-
How do direct materials affect profitability? Accurate costing of direct materials is crucial for setting appropriate prices and determining overall profitability. Overestimating or underestimating these costs can significantly impact the bottom line.
-
What are the potential consequences of inaccurate direct materials accounting? Inaccurate accounting can lead to mispricing, incorrect inventory valuations, inaccurate financial reporting, and potential legal issues.
Practical Tips
-
Implement a robust inventory management system: Utilize software or spreadsheets to track material usage, inventory levels, and costs.
-
Regularly conduct physical inventory counts: This helps to reconcile book inventory with actual inventory, identifying discrepancies early.
-
Employ appropriate cost allocation methods: Choose a method that aligns with your business needs and accounting standards.
-
Establish strong internal controls: Implement procedures to prevent theft, loss, and inaccurate recording of materials.
-
Analyze material usage patterns: Identify areas where material waste can be reduced through process improvement or material substitution.
-
Regularly review and update your inventory policies: Adjust your policies based on changes in demand, supply, and material costs.
-
Utilize technology: Implement software solutions to automate tasks such as purchase orders, receiving, and inventory tracking.
-
Collaborate with suppliers: Establish strong relationships with suppliers to ensure timely delivery and consistent quality of materials.
Final Conclusion
Understanding and effectively managing direct materials is a critical component of successful business operations. From accurate costing and inventory management to informed decision-making and compliance with accounting standards, the significance of direct materials accounting cannot be overstated. By implementing the practical tips and strategies outlined in this guide, businesses can enhance their financial performance, improve operational efficiency, and build a more sustainable and profitable future. The detailed insights provided empower businesses to move beyond mere compliance and embrace direct materials management as a strategic lever for growth and success.
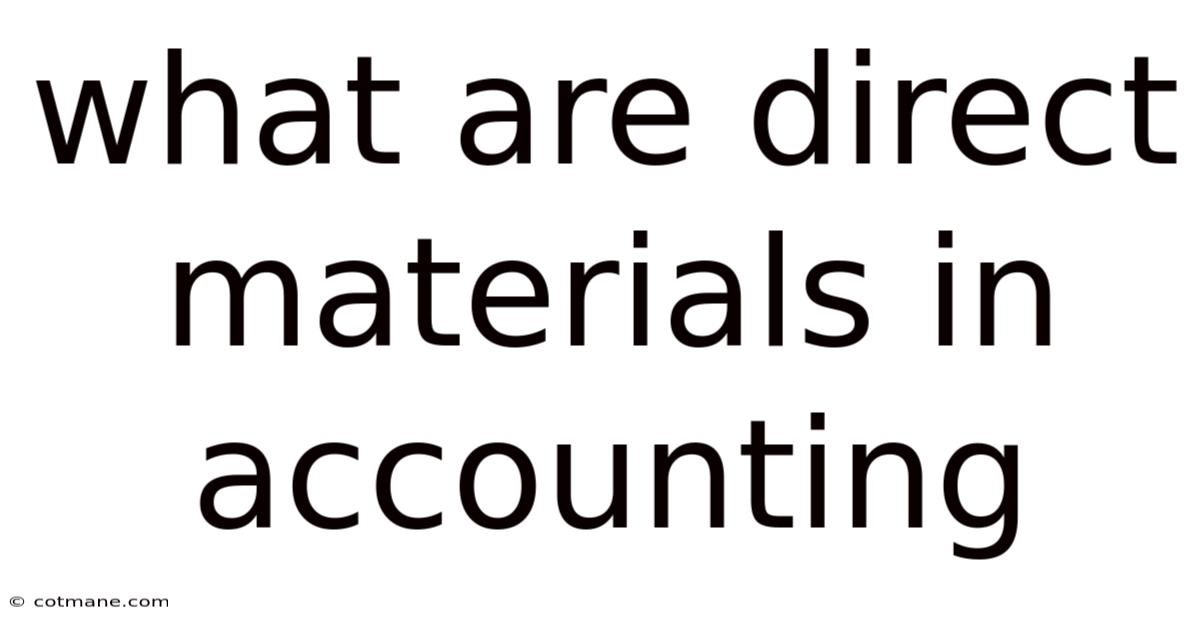
Thank you for visiting our website wich cover about What Are Direct Materials In Accounting. We hope the information provided has been useful to you. Feel free to contact us if you have any questions or need further assistance. See you next time and dont miss to bookmark.
Also read the following articles
Article Title | Date |
---|---|
What Is Analysis Paralysis Definition Risks And How To Fix | Apr 04, 2025 |
Lease Vs Rent Key Differences Similarities | Apr 04, 2025 |
How To Short A Stock For Maximum Profit | Apr 04, 2025 |
How To Recover Stolen Cryptocurrency | Apr 04, 2025 |
How To Make A Cryptocurrency Wallet | Apr 04, 2025 |